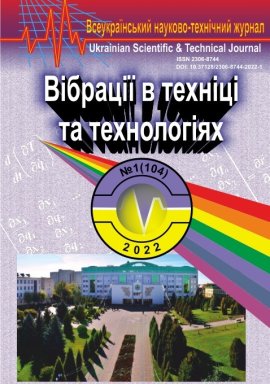
Issue №: 1(104)
The journal deals with the problems of vibration technologies and machines, mathematical methods of vibration process studies, information on design and technological development, presents teaching and methodological aspects of teaching in the Higher School of Applied Sciences, where vibration machines and technologies are studied.
SIMULATION OF FATIGUE CRACK GROWTH DURING TRANSVERSE VIBRATIONS OF A TURBINE SHAFT
Bovsunovsky Anatoliy – Doctor of Technical Sciences, Professor, Professor of the Department of Heat Power Engineering of National Technical University of Ukraine " Igor Sikorsky Kyiv Polytechnic Institute ", 03056, 37 Peremohy Ave., Kyiv, Ukraine; e-mail: apbovsunovsky@gmail.com).
Nosal Oleksandr – PhD student of the Department of Heat Power Engineering of National Technical University of Ukraine " Igor Sikorsky Kyiv Polytechnic Institute ", 03056, 37 Peremohy Ave., Kyiv, Ukraine; e-mail: oleksandrnosal1998@gmail.com
In real operational conditions structural elements of steam turbines are subjected to a wide range of thermal and mechanical loading. Even substantial reserve of static and dynamic strength, laid down at the stage of turbine design, can not prevent the appearance of fatigue cracks in structural elements, which lead to catastrophic failures. One of the reasons of damage in structural elements of turbine is technological operations used in the process of manufacture (forging, turning, and milling, heat treatment), since they are accompanied with plastic deformation of material, which is the physical basis of the so-called distributed fatigue damage. It accumulates during long-term cyclic deformation and turns into local damage of a fatigue crack type. In addition, the appearance of cracks in turbine shafts is caused by complex geometry, that is, by the presence of fillets and grooves, which are stress concentrators and, therefore, potential areas of initiation and growth of fatigue cracks. The high pressure rotor of the K-200-130 steam turbine was used to simulate the process of crack growth at forced transverse vibrations of the rotor when it passes through the first critical speed. At this the amplitude-dependent energy dissipation typical for metallic materials was taken into account. There was estimated the maximum stresses arising in the rotor when it passed through the critical speed rotation and the number of loading cycles leading to the crack growth. It was assumed that a crack with a depth of about 1 mm has formed on the surface of the rotor, which is the maximum permissible depth according to the instructions for safe operation of the turbine. The growth rate of this crack is predicted based on the fracture mechanics approaches through the determined maximum stresses in the section with a crack and experimental dependences of the crack growth rate on the stress intensity factor range. Based on the model, the crack growth time is predicted until the rotor loses its bearing ability. Predictions are made for different scenarios of loading and mechanical properties of rotor steel.
1. Troshchenko V.T., Khamaza L.A. (2018). Fatigue fracture stages of metals and alloys and stage-to-stage transition criteria. Strength of Materials, 50(3), 529–539.
2. Zhou T., Xu J., Sun Z. (2001). Dynamic analysis and diagnosis of a cracked rotor. Trans. ASME. J. of Vibration and Acoustics, 123(4), 539–543.
3. Bovsunovsky A.P. (2015). Fatigue damage of steam turbine shaft at asynchronous connections of turbine generator to electrical network. Journal of Physics: Conference Series 628 conference 1, 012001.
4. Kramer L.D., Randolph D.D. (1976). Analysis of the Tennessee valley authority, Gallatin unit N2 turbine rotor burst. In: ASME-MPC Symp. on Creep-Fatigue Interaction, pp. 1.
5. Zagretdinov I.Sh., Kostyuk A.G., Trukhnii A.D., Dolzhanskii P.R. (2004). Failure of the 300 MW turbine unit of the state district power station at Kashira: causes, consequences and conclusions. Thermal Engineering, 5, 5–15.
6. Bovsunovsky A., Surace C. (2015). Non-linearities in the vibrations of elastic structures with a closing crack: A state of the art review. Mechanical Systems and Signal Processing, 62-63, 129–148.
7. Edgar J. Gunter. (2006). Unbalance response and field balancing of an 1150-MW turbine-generator with generator bow. In: 7 th IFToMM-Conference on Rotor Dynamics, pp. 25–28.
8. Chernousenko O.U., Ryndiuk D.V., Peshko V.А. (2020). Ocinka zalyshkovogo resursu ta podovgennia ekspluatacii parovyh turbin velykoi potugnosti (chastyna 3). Kyiv: NTUU «KPI im. Igoria Sikorskogo».
9. RD 10-577-03. Tipovaia instrukcia po kontroliu metalla I prodleniu sroka slugby osnovnyh elementov kotlov, turbin I truboprovodov teplovyh elektrostancii. (2003). Moskva: Gos. unitarnoe predpriatie «Nauchno-technicheskiy centr po besopasnosty d promyshlennosni Gostehnadsora Rossii».
10. Broek D. (1988). The practical use of fracture mechanics. Dordrecht/Boston/London: Kluwer Academic Publishers.
11. Sorokin E.S. (1954). K voprosu neuprugogo soprotivlenia stroitelnyh materialov pri kolebaniah. Moskva: Gosudarstvennoe isdatelstvo literatury po stroitelstvu i literature.
12. Babakov I.M. (1968). Teoria kolebanii. Moskva: Glavnaia redakcia fis.-mat. literatury.
13. Shul’zhenko M.G., Gontarovskyi P.P., Garmash, N.G. (2010). Thermostressed state and crack growth resistance of rotors of the NPP turbine K-1000-60/1500. Strength of Materials, 42(1), 114–119.
14. Stress intensity factors handbook. (1987). In: 3 vol. Vol. I. – (Editor-in-chif Y.Murakami), The Society of Materials Sci., Japan and Pergamon Press.
15. Shlyannikov V., Kosov D., Fedorenkov D., Xian-Chen Zhang, Shan-Tung Tu. (2021). Size effect in creep–fatigue crack growth interaction in P2M steel. Fatigue & Fracture of Engineering Materials & Structures, 44(12), 3301–3319.
16. Pisarenko G.S., Iakovlev A.P., Matveev V.V. (1971). Vibropogloschaiuschie svoistva konstrukcionnyh materialov. Kiev: Naukova dumka.
17. Bovsunovskii A.P. (2011). Experimental studies on high-cycle fatigue and damping properties of R2MA rotor steel in torsion. Strength of Materials, 43(4), 455–463.
About journal
The journal "Vibrations in engineering and technology" presents materials on the following issues
• Theory of processes and machines
• Mechanical Engineering and materialprocessing
• Processing and food production
The journal "Vibrations in Engineering and Technologies" is included in the list of technical scientific publications of Ukraine
(Category "B", Order of the Ministry of Education and Science of Ukraine dated July 2, 2020 No. 886)
Old version of the site: http://vibrojournal.vsau.edu.ua/
The journal "Vibrations in Engineering and Technology" is indexed by the following databases and catalogs:
The certificateof massmedia State registration:kv no 16643-5115 from 30.04.2010 .
Founder of the journal: Vinnytsia National Agrarian University
Kind of publication: journal
Type of publication : Scientific
Publication status: Domestic
Year of founding:
Periodicity: 4 times a year
Extent: 18.75 nominal printed pages
ISSN: 2306-8744 (printed version), (online)
Language of edition : (mixed languages) Ukrainian, English
The scope of the distribution and the category of readers: national, foreign, teaching staff, scientists, businessmen.
Periodical is included in the list of scientific professional editions of Ukraine approved by the Order of Ministry of Education and Sciences of Ukraine from 21.12.2015 No. 1328.
The journal "Vibrations in engineering and technology" is included in the "Catalogue of periodicals of Ukraine".
Journal subscription can be executed in each post office department.
Subscription Index is 99720.
Old version of site: http://vibrojournal.vsau.edu.ua/
In June 1994 the 2nd International Scientific and Technical Conference "Application of vibrations for technological purposes" was organized on the basis of Vinnytsia State Agricultural Institute. Leading experts in this field, noting the significant contribution to the school of Vibration Engineering under the leadership of P. S. Bernyk, proposed to create a professional all-Ukrainian scientific and technical journal "Vibration in engineering and technology..The journal was foundedat Vinnytsia State Agricultural Institute and P.S. Bernyk was elected to be the chief editor .
For all these years (since 1994) theJournal "vibration in engineering and technology" published 94 issues wherestudy of vibration effects, the creation of progressive energy saving technologies and equipment for their implementation were highlighted.
Currently Kaletnik H.M PhD , professor, academician NAAS is the chief editor of the "Vibrations in engineering and Technology"
The journal "Vibration in Engineering and technology", which has no analogues on the territory of Ukraine, is well known abroad.